PUBLISHED BY DiPaolo CNC
How to Plan for Plant Maintenance
It's not uncommon for factories to have scheduled maintenance shut-downs at various points each year. During this time, the plant floor gets cleaned, equipment is checked or replaced, processes get improved, and production lines get added. Regardless of the work that is to be undertaken, this "off-line" time can either hurt or help your business, depending on how well you plan and execute the planned outage. We've identified the 5 phases of planned shutdowns to help you plan for success. Let's take a look!
Phase I: Define and Implement Strategies for Plant Maintenance Shut-Down
- Analyze the frequency and duration of plant maintenance shut-down.
- Assess the best time for a shut-down in relation to manufacturing forecasts.
- Determine the key drivers of the shut-down, such as improving equipment and complying with health and safety codes.
- Appoint a steering committee to lead the shut-down and assess the impact on company goals.
- Make a list of equipment parts that require maintenance or improvement.
Phase II: Plant Maintenance Shut-Down Preparation
- Develop plans for how the maintenance will be performed.
- Adjust environmental, health, and safety plans to incorporate the improvements.
- Determine the logistics of materials and resources needed for the shut-down.
- Develop plans for quality assurance.
- Create contingency plans for any risks or problems that may arise.
- Complete necessary pre-shut-down jobs.
Phase III: Execution of the Project
- Assess and address any unforeseen issues that arise during the shut-down.
- Manage internal and external resources efficiently.
- Update the work package schedule daily and track data for comparison with Key Performance Indicators (KPIs).
- Test the improvements and repairs made during the shut-down.
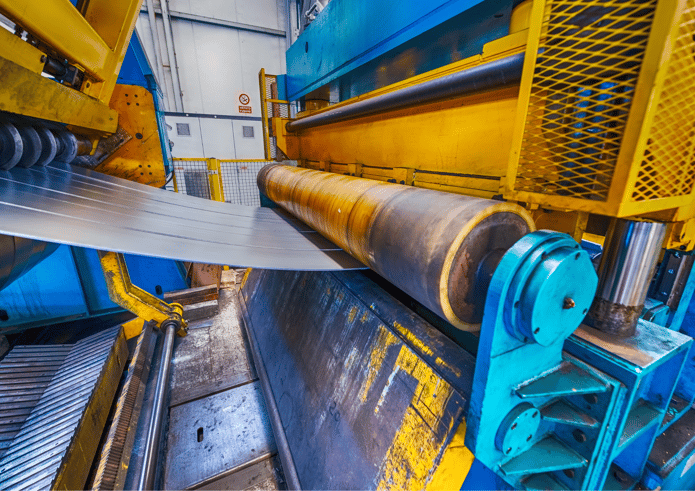
Phase IV: Start Up & Turn Over
- Handoff the new system to the operations team for testing.
- Perform trial runs to observe equipment performance and make adjustments.
- Complete a final walk-through to assess completed and outstanding tasks.
- Demobilize the work site and dispose of unused resources.
- Host a post-mortem meeting to evaluate the success of the shut-down and learn from the experience.
- Tie up loose ends, close financial paperwork, and analyze costs.
Phase V: Evaluation
- Monitor the equipment that was improved during the shut-down.
- Continuously improve documentation and best practices for future shut-downs.