How The Right CNC Machine Tools Benefit Your Business
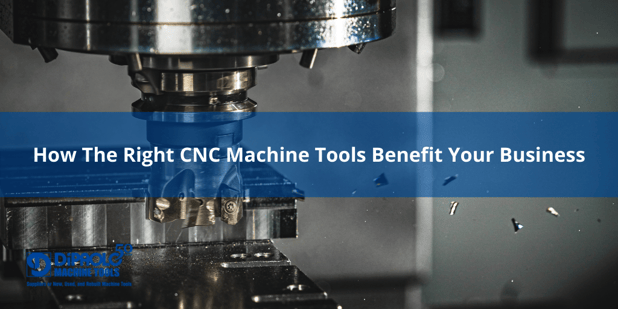
Looking to find the right CNC machine tool to boost your factory’s productivity?
Doing so can be challenging. You have to tick off multiple factors. They include cost, space, part complexity, materials to be machined, as well as how you should set up the machine tool in your premises.
And let’s not forget about manpower — is your machinist skilled enough to operate and maintain your newly acquired and preferably more advanced machine?
There is much to gain from learning about why CNC machining matters in manufacturing as well as the benefits of choosing the right CNC machine tool for your manufacturing needs.

CNC Machining In Manufacturing
CNC machining involves manufacturing with speed, precision and flexibility in mass or batch production. Due to their powerful capabilities, CNC machine tools are used in all kinds of industries to produce countless components.
The automobile, camera, arms and aerospace industries were some of the first to use CNC machining. In the case of aerospace industry, they were able to tap on the ability of CNC machines to manufacture lightweight parts with very tight tolerances, allowing aerospace components to be made even out of the most difficult materials. These include fuel access panels, engine mounts, landing gears, engine housing, turbine wheels, plates and other parts.
CNC machines are also regularly used in the automotive industry to make parts of gear boxes, valves, cam shafts, brake discs, engine blocks and cylinder heads, pistons, and body panels. Beyond these, electronic items and even dashboard panels and headlights could be produced by selecting the right CNC machine tool.
CNC machining is highly valuable to the medical industry. This is due to its complexity and ability to machine parts to very tight tolerances, ensuring accuracy in making high precision surgical and equipment components such as X-Ray machines, scanners, microscopes, and transfusion equipment. Even human spare parts made out of materials such as titanium hip joints, knee caps, teeth implants, and bone screws can be manufactured with high precision CNC machines.
The oil & gas industry is another heavy user of CNC manufacturing techniques. With their wide range of uses, CNC lathes or machining centres can be used for fabricating precise and reliable parts such as connectors, pumps, pipes, Christmas trees, drilling tools, casings, shafts, cylinders, and valves.
CNC machining is also widely used as an indirect manufacturing process to create molds & dies. Molds will be injected with molten plastic or filled with liquid casting material to form machinery parts. Dies, on the other hand, will be injected with aluminum or other materials to create products in large quantities. All molds & dies are machined with utmost precision by CNC machining centres. CNC machining applications are also used in other industries such as the semiconductor, construction, ship building, and wind power industries. Even common items which you use daily are bound to have components produced by CNC machines — these include smart phones and IT products, home appliances, sport shoes, washing machines, vacuum cleaners, and remote controls.

What Are The Benefits Of The Right CNC Machine Tool
Increased Manufacturing Productivity
The most prominent benefit of using CNC machining is its easy and accurate repetition from manufacturing part to part as well as its production speed. By computerizing the instructions and pre-setting its actions, countless components can be made — each and every one of them will be exactly the same. Major production operations can also be automated to increase manufacturing efficiency, speed and productivity while optimizing quality, stability and profitability. The use of highly rigid CNC machine tools (barring any malfunction or maintenance issues) allows shop floors to work continuously. Given the right conditions, CNC machines can work 24/7 — including during weekends and holidays — and only stopping for needed maintenance or repairs. This greatly increases your factory’s productivity and efficiency.
Improved Shop Floor Productivity
With CNC machine tools, factories no longer have to invest in specific production lines using step-by-step production methods with different machines to complete specific parts. This leads to a reduced floor space, lower utility bills, and more efficient deployment of manpower.
Extreme Precision And Accuracy
With multiple programmable attributes, every detail, specification and design of the production process can be fed into the machine, leaving no room for error. This unlocks multiple possibilities that were previously impossible to produce through manual processes.
High quality CNC machines can achieve incredible accuracy and tight tolerances. The standard tolerance of any dimension in CNC machining today is ± 0.01 mm. Features with tighter tolerance down to ± 0.005 mm can be manufactured — even tolerances of ± 0.002 mm are possible with the right machine tools. With the latest NANO technologies which split microns into many more steps, even tolerances that are invisible to the naked human eye can be achieved.
Flexible Production
CNC machine tools provide the flexibility to produce almost any part, allowing machining operations to keep up with shifting customer demands across multiple industries. Some of the latest CNC machine tool models include features and accessories that further expedite and simplify the production process, for example Automated Tool Changers (ATC). CNC machine tools can also be used in conjunction with other manufacturing equipment and processes to form part of a flexible manufacturing system in your factory.
Product Consistency
The right machine tool provides more manufacturing options. It ensures that the design and quality of the components remains the same regardless of whether you’re machining just a few parts or thousands of the same pieces. With this flexibility, you can decide exactly how many parts you need at any given moment and reduce excess inventory.
Parts Complexity
When used with compatible CAD / CAM programs and tools, CNC machine tools can produce complex and intricate parts that go far beyond the abilities of manual machining.
Factory Safety
CNC machines can help to minimize workplace accidents with their inbuilt safety features. These may include emergency stop buttons, bullet proof casings, curtain guards and safety panels, as well as systems that can run diagnostic tests prior to each operation.
Lower Long-Term Costs And Higher Profitability
The collective result of CNC machine’s higher speed, productivity and most of all, lower labor costs, all add up to a better bottom line for your business.

How To Choose The Right CNC Machine Tool
There are many factors to consider when you choose the right CNC machine tool for your factory. To ensure that you select the right CNC machine tool for your manufacturing needs, do follow these seven points:
- Check Your Current Machine Tool Set-Up and Operator Experience
- Check Your Part Difficulty and Complexity
- Identify Materials to Be Machined
- Consider Either Linear Motion (LM) Guide Ways or Box Guide Ways
- Evaluate the Types and Capability of CNC Control System
- Calculate the Cost Per Part
- Measure the Available Space at Your Factory
You should also evaluate if CNC machines can be upgraded with Automation Solutions to drastically increase productivity and reduce the intensity of manpower. Automating machining processes simplifies your production process, allowing your factory to produce more precise parts at higher accuracy and speed.
For help on choosing the right CNC machine tool, you can contact us here.
Conclusion
Investing in the right CNC machine tool for your factory can yield significant benefits to your business.
Combining the state-of-the-art technology with flexibility in machining various components, CNC machine tools like 5-axis machines are well-suited to meet the latest trends in manufacturing.
In general, parts are becoming more and more complex and demanding to produce. Batch sizes are smaller with frequent returns, demanding a high grade of flexibility.
To learn more about the different types of machine tools available and to choose the best options available, feel free to reach out to us!